Jeudi 31 janvier 2019 / Journée 2 / Acte 1
Quels projets, pour quelle filière de demain ?
Interventions de
- Marion Sanglard, HES Bernoise, Institut des matériaux et de la technologie du bois
- Stefan Zöllig, DG de TS3 et Timber structures 3.0 fondateur de Timbatec ingéneurs bois
- Nicolas Henchoz, Directeur du laboratoire EPFL, Ecole cantonale des Arts de Lausanne (EPFL+ECAL LAB)
- Fabienne Favre Boivin, HES d’ingénierie et d’architecture de Fribourg
- Cyril Jiguet, Co-fondateur et directeur de production de Weden
- Lucile Delaunay-Driquert, Weidmann Group
De matériau classique, le bois se transforme en ressource du futur, transcendant largement ses vocations traditionnelles de lieu propice à la détente, de combustible, ou de matériau destiné à la décoration intérieure. On découvre aujourd’hui, grâce à la recherche fondamentale et appliquée, son potentiel innovant. Ces champs d’application concernent bien entendu la construction et la production d’énergie mais aussi l’industrie chimique, celle du meuble et de l’automobile, la cosmétique, le médical et bien d’autres domaines encore. Le bois serait-il le futur du pétrole, du béton et du plastique ? Un panel de 6 chercheurs présente ici des applications prometteuses à divers degrés de maturité.
LES COLLES BIOSOURCÉES
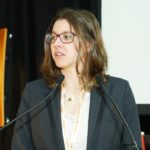
Déplacer le modèle de la pétrochimie vers de la bioraffinerie
Pour les adhésifs Phenol Formaldhéhydes (PF), deux composants toxiques, le formaldéhyde serait substitué par la molécule précédemment évoquée (5-HMF) et le phénol par de la lignine.
« La lignine est présente en quantité (on en produit 50 millions de tonnes par an et on en n’utilise que 2 %) et présente l’avantage d’être peu coûteuse. Son prix pourrait d’ailleurs très vite chuter, contrairement au formaldéhyde et au phénol dont les cours sont à la hausse. » — Marion Sanglard
Le projet, financé en partie par la confédération (Partenariat public/privé) s’est révélé très concluant, et le procédé devrait passer du laboratoire à la pratique. Encore faut-il, et c’est une autre bataille, convaincre les industriels d’adopter une attitude volontariste et d’adapter leur technologie de production. La substitution totale des colles par ces colles naturelles paraît inéluctable mais nul ne sait le temps que cela prendra. Sans doute le recours à l’interdiction totale de colle à base de formaldéhyde de la part des autorités viendra-t-elle un jour cesser les tergiversations… À moins que l’augmentation du prix du pétrole n’ait raison d’elles avant cela.
REMPLACER LE BÉTON DANS LA CONSTRUCTION
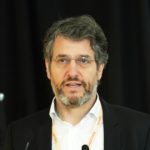
TS3 est en réalité une technologie (Timber Structure 3.0). « TS3 est la troisième génération de la construction bois en quelque sorte » explique Stefan Zöllig.
Cette dernière était jusque là la seule à pouvoir de créer des éléments structuraux, comme des dalles, capable de supporter des charges dans plusieurs directions.
« Les résultats obtenus jusqu’à présent confirment que la construction de plafonds plats en bois, avec une grille d’appui allant jusqu’à 8 × 8 m et une charge utile de 500 kg/m2, est désormais possible »
TS3, une technologie révolutionnaire dans la construction en bois
« Avec cette technologie, 2500 m2 ont déjà été réalisés notamment des immeubles d’habitation à Grossaffoltern près de Berne tandis que et 100 000m2 sont en préparation ». Le procédé est donc mûr pour le marché. Les ingénieurs espèrent obtenir en automne 2019 l’approbation de l’Union européenne et des États-Unis pour lancer sur le marché mondial des dalles bois, auparavant réalisées en béton armé, un enjeu colossal correspondant à une part de marché de un à cinq pour cent – sur un marché d’un milliard de dollars.
Grâce à la technologie Timber Structures 3.0 (TS3), des éléments en bois peuvent être solidement assemblés par collage frontal, permettant ainsi la fabrication de barres et de panneaux de toutes formes et de toutes tailles.
Cette nouveauté mondiale a été mise au point par la société Timber Structures 3.0 AG en étroite coopération avec la BFH-AHB Bienne, l’Ecole polytechnique fédérale de Zurich, Purbond AG, Henkel & Cie AG, Schilliger Holz AG et la société Stuberholz AG, Schüpfen.
TS3 permet d’édifier des constructions de plusieurs étages par assemblage de piliers et panneaux suivant une grille pouvant atteindre 8 × 8 m et avec une charge utile de 500 kg/m2.
LA DENSIFICATION : POUR RENDRE L’ÉPICÉA AUSSI DUR QU’UNE ESSENCE RARE
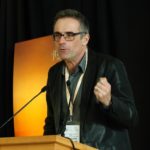
De ce dialogue entre design et science émerge un nouveau matériau : le bois densifié.
Technique de densification du bois
La densification a pour principe de transformer un bois tendre, comme l’épicéa (densité 0.5) en un bois dense comme les essences précieuses d’Amazonie (densité 1.5), au moyen d’un traitement complexe basé sur la chaleur, l’humidité et la pression, le tout sans avoir recours à une substance chimique.
La composition demeure entièrement naturelle et permet à la fois à des bois courants d’acquérir les performances de certains bois tropicaux et de se doter d’une texture exceptionnelle offrant la douceur d’un polissage parfait.
Simple de prime abord, l’objet surprend en réalité par sa complexité de conception.
Le designer hollandais souhaitait utiliser du noyer afin de réaliser cette idée cannibale, de l’arbre qui casse son propre fruit.
« Il a fallu toute la patience du scientifique et l’espoir sans faille de l’artiste pour que naisse, dans ce nouveau matériau, l’objet utilitaire ».
La capacité de mise en forme par des moulages et le travail sur la stabilité de la transformation a constitué un défi majeur. Les fibres suivent la forment de l’objet et les propriétés techniques peuvent être ajustées comme c’est le cas pour les chaussures sur lesquelles il a été pratiqué une densification différentielle : près de la semelle, la densification est de 20% car il était nécessaire de garder de la légèreté et de la stabilité tandis qu’à la pointe, il fallait de la densité et de la résistance à l’abrasion (100%). Tous ces objets montrent que le champ d’application est très large.
Pendant 6 mois l’équipe a bénéficié d’une vitrine magnifique avec la présentation des objets au Musée des Art Déco de Paris et a profité d’un très gros impact notamment auprès d’entreprises prestigieuses telles Hermes, Vuitton ou Vitra. Mais ces dernières achètent des pièces et ne se présentent pas comme des partenaires industriels qui font encore défaut. « Le travail doit à présent se focaliser sur l’industrialisation du procédé afin pour que le bois densifié sorte du musée et des laboratoires et intègre notre quotidien ». À bon entendeur.
LE BOIS POUR L’ÉPURATION ET LE TRAITEMENT DES EAUX

Il existe plusieurs domaines de l’eau : les eaux usées, les eaux de recharge de nappe, et les eaux de ruissellement pour lesquels des législations ou des besoins de traitements sont apparus.
Macropolluant contre micropolluant
Macropolluant: Il s’agit de matières en suspension, de matières organiques et de nutriments comme l’azote ou le phosphore. Ils peuvent être présents naturellement dans l’eau, mais les activités humaines augmentent la concentration des macropolluants dans les rivières.
Micropolluant : Un ensemble de substances chimiques qui contrairement aux macropolluants, sont toxiques à très faibles doses. Il peut s’agit de pesticides, résidus de médicaments, hormones, etc.
La recharge des nappes se fait par réinfiltration artificielle d’eaux de surface. L’une des plus emblématiques est sans doute la nappe de San Fernando pour la ville de Los Angeles.
Le même principe est également appliqué à côté de chez nous, avec la nappe de l’Arve qui est rechargée par les eaux de l’Arve sous la surveillance des services industriels de Genève (SIG), avec un pré-traitement classique mais qui n’élimine pas les micropolluants. « Donc la question de l’utilisation d’absorbants pour le traitement de ces micropolluants avant la réinfiltration se pose légitimement. »
Recharger de façon artificielle un aquifère à partir des eaux de surfaces
Les eaux de ruissellement
Dans le domaine des eaux de ruissellement, il existe aussi depuis 2002, une nouvelle pratique qui demande à ce que les routes qui subissent un fort trafic subissent un traitement des eaux de ruissellement avant leur liberation dans leur milieu naturel.

Les eaux ruisselant sur les routes fortement fréquentées sont chargées en polluants provenant de l’usure des freins, des pneumatiques et de la chaussée. Leur évacuation soignée est impérative pour protéger les eaux.
Fabienne Favre Boivin explique avoir d’ailleurs participé à un projet de recherche en collaboration avec hepia sur une solution innovante pour le traitement des eaux de ruissellement à la fois très performante et très compacte au moyen de biochars issus de déchets de bois. Il s’agit de « Technosols » avec 70% de biochars de déchets de bois urbains: 100 kg/m linéaire pour une route à 3 voies. (Projet SMACC, HEAI-Fr et hepia).
Voies CFF
De même l’évacuation contrôlée des eaux des installations ferroviaires est nécessaire car l’utilisation de lubrifiants et d’herbicides le long des lignes ferroviaires représente un risque certain de pollution pour les eaux. (Projet CFF en cours: HEIA-Fr et hepia)
Qu’est ce qu’un biochar ?
Ce sont des matériaux analogues aux charbons actifs, des absorbants capables de fixer les molécules dont on veut se débarasser dans les eaux. Ils proviennent de différents types de biomasse : du bois de différentes essences, de différentes parties du bois (déchets de bois : sciures, écorces, branchages, souches…) ou n’importe quelle autre biomasse dont on n’a pas d’application vivrière. La condition pour que ce soit un biochar est qu’il soit produit avec un bilan carbone proche de zéro. Ils sont produits grâce à la pyrolyse, une combustion à très haute température et en l’absence d’oxygène dans des unités de production très artisanales ou très industrialisées.
Le biochar dispose de propriétés analogues à celles d’un charbon actif, sa capacité de fixation des polluants variant en fonction du choix de la biomasse de départ et des conditions de pyrolyse (temps, températures…). C’est une véritable alternative locale au charbon actif d’importation.
Pyrolysis reactor Pyreg 500

Besoin du marché de l’épuration des eaux : 10 000 tonnes de biochar par année (estimation). C’est un besoin très important qui est pour le moment comblé par les charbons actifs d’importation.
Le projet Sylvo est né du constat que ces traitements allaient nécessiter la consommation de milliers de tonnes de charbon actif par année alors que les récentes études montrent qu’il semble possible d’utiliser des biochars produits à partir de biomasses locales pour le même niveau de traitement que les charbons actifs.
Impact et portée territoriale du projet SylvO
L’objectif du projet Sylvo est ainsi d’étudier, sous l’angle scientifique/économique et environnemental/ technique et industriel, dans quelle mesure les sous-produits des bois locaux peuvent produire un biochar à forte capacité de dépollution pour l’élimination de micropolluants dans l’eau, conformément au cadre réglementaire en émergence.
Le projet franco-suisse, s’appuyant sur (HEIA-Fribourg / Technopole d’Archamps pour les chefs de file) s’inscrit pleinement dans le domaine d’excellence du territoire, d’utilisation efficace des ressources et des matières premières, et répond à un objectif de protection et de valorisation du patrimoine naturel.
Sylv0 : Ojectifs généraux
- Valorisation des produits et sous-produits de l’industrie du bois sous forme de biochars pour le traitement des eaux usées et de recharge de nappe
- Développement de la recette de pyrolyse
- Identifier les conditions économique et écologiques favorables de la filière de production de biochars à partir de produits et sous produits de l’industrie du bois
- Transfert technologique vers les producteurs de bois et les acteurs du traitement des eaux
DESIGN ET ÉCOLOGIE

« Smarter wood for smarter use »
« L’ objectif de Weden est de remplacer les matériaux traditionnels en créant des nouvelles combinaisons de bois pour des usages nouveaux et plus intelligents », explique Cyril Jiguet. « Nous avons créé un nouveau matériau, le weden, qui s’apparente à un contreplaqué doté de caractéristiques différentes : flexible, malléable et à mémoire de forme », poursuit-il.
L’objectif de base était bien de remplacer le plastique dans certain de ses usages et par conséquent, d’obtenir quelque chose qui soit flexible et à mémoire de forme. Mais l’activité de Weden ne s’arrête pas là : « nous souhaitons répondre à toute forme de sollicitations, du produit rigide jusqu’au produit très souple, en passant par tous les intermédiaires possibles, selon les usages et les besoins de chaque produit ».
Un travail sur les qualités intrinsèques du matériau mais aussi sur la forme
La recherche s’est également tournée vers une réflexion sur la forme : des formes plates qui vont s’apparenter à des contreplaqués traditionnels, des formes extrudées, apparentées au bois moulé traditionnel, ou bien des formes plus recherchées, complètement organiques. « L’idée, c’est de ne plus limiter le bois à ce que l’on connaît et d’en ouvrir les usages».
Que fait Weden ?
Weden crée de nouveaux matériaux, intègre le côté composite du bois, recherche des caracteristiques encore inexploitées de la matière, choisit les plis, les orientations, les types de matériaux et explore les différents types de collage, pour créer un produit esthétique et performant.
Conférer au bois de nouvelles performances
La recherche intervient également au niveau des critères de performances : caractéristiques mécaniques, résistance au milieu extérieur, incorporation de fonction, densités ou encore, aspects. La combinaison de l’ensemble de ces caractéristiques donne naissance à une multitude de produits déclinables selon les aspects, les propriétés mécaniques et les caractéristiques finales.
De la même manière, l’équipe d’ingénieurs a également cherché à combiner différentes matières et explorer le côté composite du bois : avec des films d’aluminium, des feuilles de pierre, etc.
« On arrive à obtenir des structures qui vont avoir des caractéristiques techniques liées au bois mais avec un aspect et un toucher qui vont plutôt s’apparenter à ceux de la pierre. Il est très intéressant d’intégrer d’autres matériaux au sein des structures pour renforcer les caractéristiques ou encore, intégrer de la fonction. » — Cyril Jiguet
Bien sur les considérations environnementales sont pris en compte dans la conception : « nous cherchons à travailler sur des solutions recyclables ou qui vont pouvoir se dégrader naturellement. Mais le point-clé, ce sont les colles. La recherche concernant le collage demeure importante ».
La question du financement
Les technologie utilisées par Weden permettent de dépasser un problème de taille, celui de l’investissement conséquent lié au moulage. « Le travail de Weden consiste à travailler essentiellement sous vide, avec des moules qui vont varier selon les étapes. Nous sommes en mesure de modéliser très vite un produit à bas coup, et ainsi à quitter le modèle en 3D. Nous pouvons maquetter rapidement ce qui a l’avantage de créer l’objet, de l’avoir dans les mains et de pouvoir le faire évoluer ».
Les secteurs d’activité concernés par le matériau n’ont pas de limite. Weden peut concurrencer le plastique, le composite dans certaines applications, le bois traditionnel, le bois moulé, couvrant une palette d’application illimitée comme le design, le mobilier, le packaging, le visual merchandising. La typologie des clients est, elle aussi très contrastée, puisque Weden peut répondre à la demande de gros groupes, de PME ou de projets individuels.
QUEL EST L’AVENIR DU MARCHÉ DES MICROFIBRILLES DE CELLULOSE ?

Présentation succincte du groupe Weidmann
Le groupe Weidmann est divisé en trois départements, Weidmann Electrical Technology, Weidmann Fiber Technology, et Weidmann Medical Technology.
- Le premier, fondateur de Weidmann, existe depuis plus de 140 ans et fabrique, à partir de cellulose (40 000 tonnes par an de pâte à papier), des composants et isolants électriques que l’on retrouve dans les transformateurs.
- Weidmann Fiber Technology. Cette deuxième division , pionnière en la matière, produit et développe les utilisation de la microfibrilles de cellulose.
- Weidmann Medical Technology. Ce département est indépendant. Il n’utilise pas la cellulose mais le plastique et est dédié au développement de composés dans le domaine médical.
Depuis 1877, le groupe Wicor (Weidmann International Corporation), dont le siège est à Rapperswil (SG), transforme des fibres naturelles en produits pour l’industrie électronique. Outre les filiales existantes que sont Weidmann Electrical Technology et Weidmann Medical Technology, la dernière née Weidmann Fiber Technology se développe au siège de Rapperswil depuis 2016. Elle a pour but de produire de la cellulose microfibrillée (MFC) en quantité industrielle et de développer des applications.
Les microfibrilles de cellulose
« Pour les obtenir, on utilise de la pâte à papier que l’on redilue dans l’eau, donnant 97% d’eau pour 3% de matière sèche. Par un procédé mécanique, on arrive à ouvrir la paroi des fibres et à individualiser et à répandre ces microfibrilles, ce qui permet d’avoir un réseau complet de microfibrilles », poursuit-elle.
« Ces réseaux de microfibrilles ont pour diamètre un nanomètre et pour longueur plusieurs dizaines de micromètres. Avec ce procédé, notre objectif est d’obtenir ces microfibrilles mais aussi de faire varier le niveau de fibrillation de la matière ainsi que d’augmenter la surface spécifique que l’on a sur les fibres. Cela permet de mettre en évidence les liaisons hydrogène/oxygène et permet de faire des modifications susccessives sur la matière. » indique Lucile Delaunay-Driquert.
Les champs d’application
En fonction de la concentration de la matière, (jusqu’à 25 %) il est possible d’obtenir différentes formes d’application, sachant qu’elle ne peut pas se trouver sous la forme solide. En effet, les microfibrilles perdraient les liaisons H-O et ne garderaient pas la même structure.
*MFC = microfibrillated cellulose
Le groupe Weidmann définit la matière en trois composés importants :
- Selon la surface spécifique, de 60 à 260m2 par gramme (élevée ou basse)
- Selon la charge de surface ( par exemple cationisée, ou TEMPO-oxydée)
- Selon la morphologie (longiligne ou fragmentée), selon les usages
Le groupe Weidmann fait également varier les composés en fonction du type de matière, obtenue à partir de :
- fibres de feuillus
- fibres de résineux
- fibres de plantes annuelles ou de fibres issues de déchets de l’agroalimentaire (peau de citron, etc.)
Applications
Les perspectives économiques sont très encourageantes et varient selon les secteurs et le degré de maturité des produits. Le développement prend en général 2 à 3 ans, et dépend aussi du temps d’acceptation du produit de la part du consommateur.
À titre d’exemple, sur le marché américain la part des microfibrilles de cellulose est estimée à 540 millions de dollars d’ici 2024.
Le groupe Weidman a pour l’instant misé sur 3 secteurs : la cosmétique, la filtration et les emballages. Il a également beaucoup investi il y a deux ans et demi, possédant aujourd’hui une capacité de production de 1600 tonnes de matière et demeure ouvert à toute forme de collaboration pour continuer la recherche et l’innovation.
Sophie Barenne